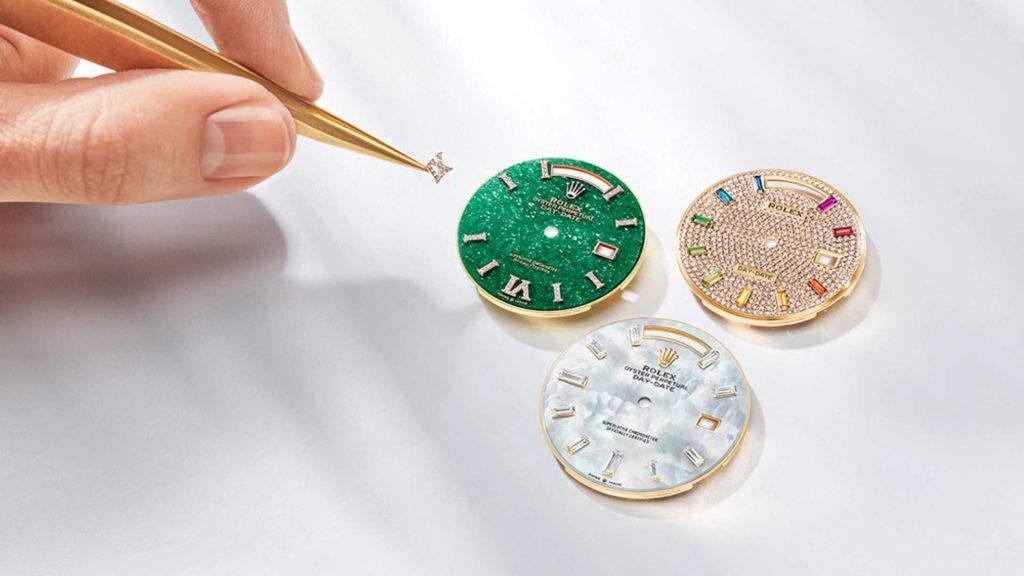
It is no surprise that the Rolex watch dials are made entirely in-house, and rightfully so, as a master of the craft. A watch is more than a time-telling tool; it’s a canvas of style and design, where the dial takes centre stage. This crucial element, often the first to catch the eye, is essential in product development, seamlessly complementing and enhancing the case and bracelet or strap with its design. Artisans add texture, pattern, and structure, transforming these pieces of metal into a masterpiece through a fusion of creativity and innovation.
The creation of the dial is an art form known as art cadranier. At its dedicated Chêne-Bourg facility in Geneva, a team of approximately 500 specialists, including gemsetters, painters, and engineers, is entirely devoted to dial-making. A discerning eye can spot imperfections as small as a tenth of a millimetre, equivalent to the thickness of a human hair.
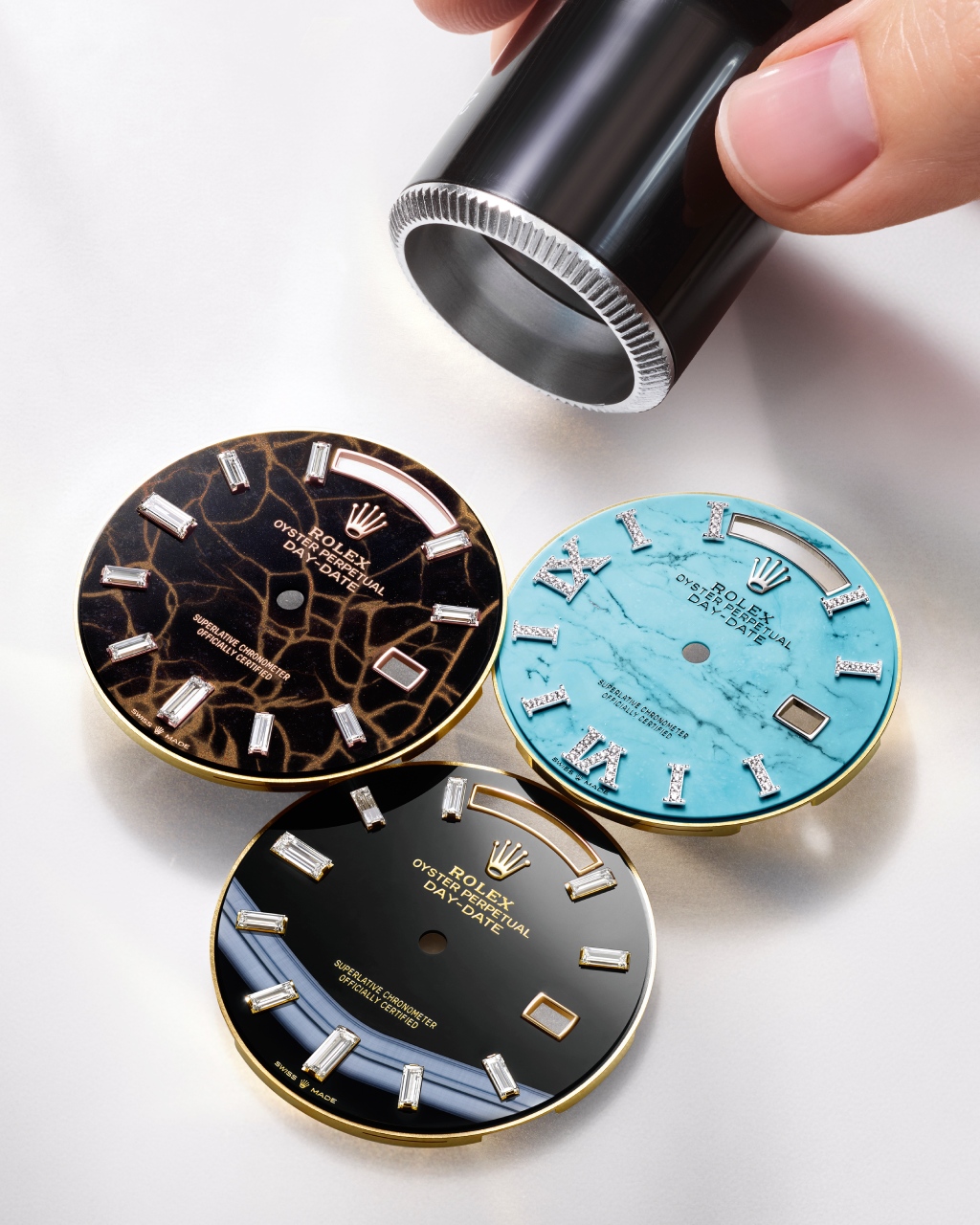
The quality of a dial serves as a telling measure of a brand’s dedication to craftsmanship. The journey begins with an original concept that undergoes rigorous revision, experimentation, and refinement, leading to the blueprint of a dial design. The dial development team, under research and development, transforms this design into a prototype through collaboration among designers, engineers, and subject matter experts. Out of hundreds of prototypes created annually, only a select few make it to the brand’s catalogue.
The dial’s primary function is to enable clear time reading under all circumstances. Starting with a brass disc, or sometimes in precious metals like 18 ct yellow gold, white gold, and pink gold no fewer than 60 operations are required to transform a metal dial into a finished dial, with some dials paved with gemstones or set with gem hour markers. These markers, crafted from 18 ct gold to resist corrosion, are either made as three-dimensional elements or pad printed. Often used to imprint text and symbols, pad printing or tampography is a technique that can also be used to create decorations such as the whimsical ‘Celebration’ motif introduced in the Oyster Perpetual range last year.
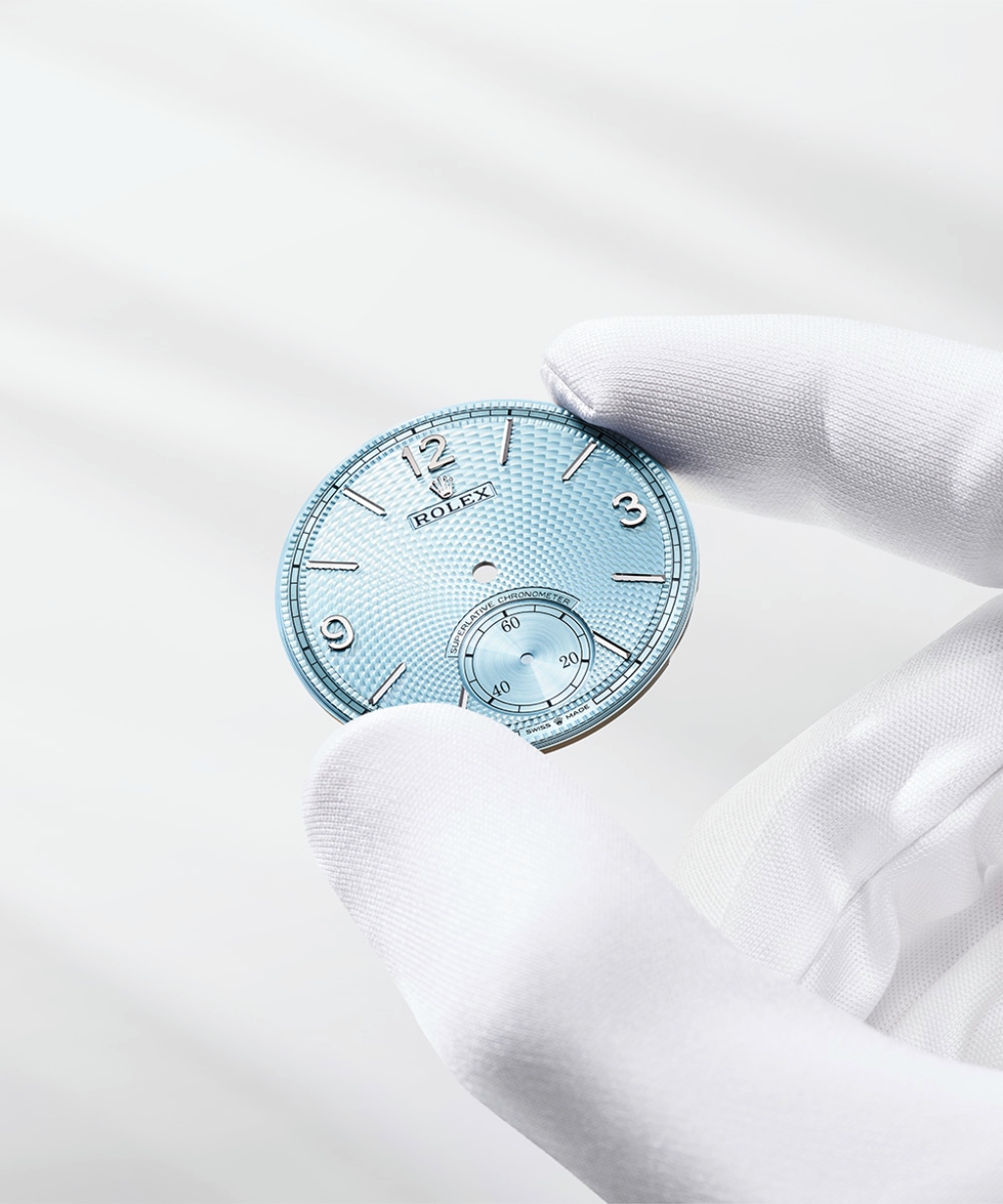
Rolex is renowned among watch connoisseurs for its exquisite dials made from natural materials like opal, onyx, turquoise, and meteorite. These materials are meticulously selected, with Rolex teams visiting mines worldwide for sourcing. Each material disc is inspected for smoothness, flawless structure, and harmonious colours before being mounted on brass dial plates. These unique materials enrich Rolex’s collection with diverse textures and hues. Some models feature dials partially or fully paved with diamonds, individually hand-set onto 18 ct gold bases. This meticulous craftsmanship enhances the luxury and distinction of these timepieces.
To achieve a dozen exclusive coloured dials, a suite of specialised techniques is employed. Lacquering involves airbrushing pigment onto the dial in fine layers, producing a spectrum of bold, opaque colours. Electroplating thin layers of metals creates shades like silver, champagne, slate, and steel. PVD (Physical Vapour Deposition) goes beyond electroplating, covering the dial with metal oxide alloys or nitrides in a layer less than a micron thick, resulting in rich colours like olive green and chocolate, or subtle hues like ice blue and pink. Grand feu enamelling, a complex métier d’art, is used for intricate dial decoration, yielding intense colours that remain vibrant over time. Beyond colour, the final surface finish of the dial also influences its appearance. A sunray finish, composed of fine radial lines, or a satin finish, made up of minute parallel lines, creates different effects as light strikes the dial.
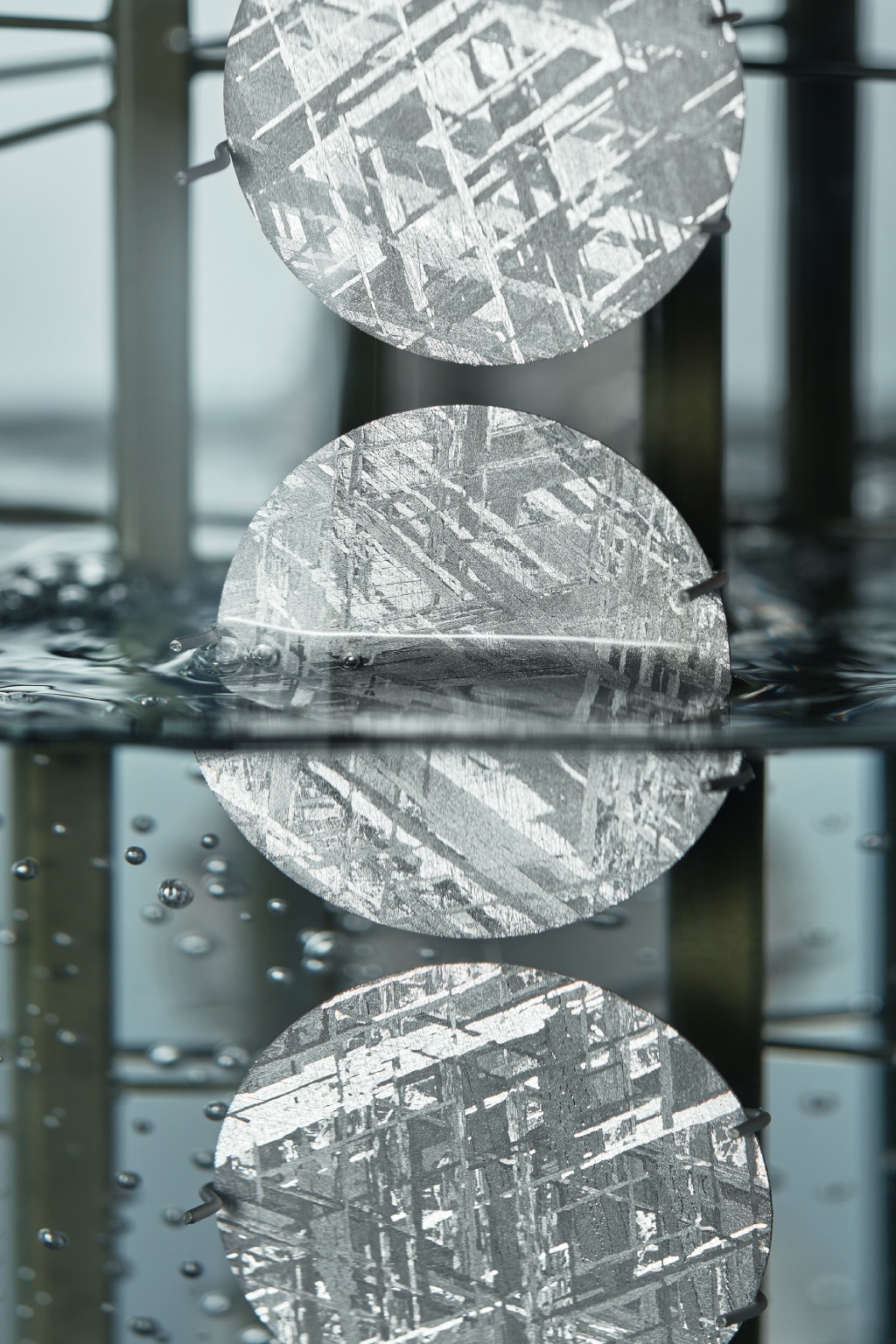
Even with dials of the same colour, a matte varnish exudes sporty energy, while a glossy varnish channels sophistication. In the final stages of production, skilled artisans delicately attach the appliques—including hour markers and the iconic Rolex crown—to the dial by hand. Carefully inserting each piece’s feet into pre-drilled holes, operators shield their tweezers with paper to prevent any risk of scratching. Using a press applying 80 newtons of pressure, the feet are securely riveted to the dial. Before this meticulous process, each hole is precisely machined with a counterbore of one-tenth of a millimetre, ensuring the metal is perfectly accommodated and secured during riveting.